Just-in-Time (JIT) Inventory Management: Definition, Pros & Cons
Just-in-Time (JIT) inventory has been around since the 1970s. Business owners love it because it lowers their storage costs, reduces waste, and increases efficiency. It allows you to keep only the required amount of raw supplies on hand. Allowing companies to meet demand without keeping large stockpiles of inventory.
Table of Contents
KEY TAKEAWAYS
- JIT lowers the cost of carrying inventory and makes businesses leaner.
- Lower production levels mean better quality and fewer defects.
- It’s difficult to meet large bumps in demand without a stock of inventory.
What Is Just-in-Time (JIT)?
Just in time is a production philosophy where manufacturers produce goods as they’re ordered. Goods are not produced in advance and stocked. Instead, they’re produced as the customer orders them. Raw materials are in minimal supply to keep storage costs low.
Toyota Motor Corporation made this strategy popular in the 1970s. It took them decades to perfect the process. But it became one of many factors that helped them become a leader in the auto industry.
Companies today adopt a JIT inventory model to become more lean and efficient. Are you storing raw materials and making products that go unsold for months? If your business is looking to cut excess and drop reordering, this could be a good solution.
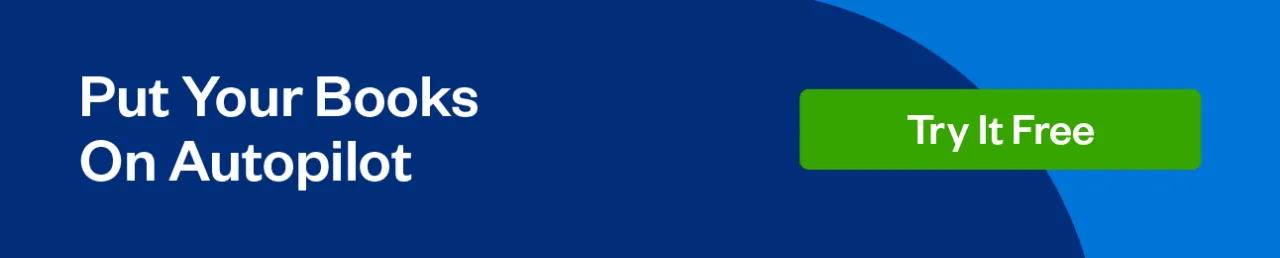
The Purpose of JIT
The goal behind JIT inventory strategies is to keep enough supplies on hand to meet sales needs and nothing more. By only buying what the company needs you meet several goals. Overall, the broadest purpose of a JIT system is increasing profitability.
The system accomplishes this main goal in a few ways:
- It keeps low levels of production making it easier to spot defects. This lowers the number of scrapped products and increases efficiency.
- Small frequent material orders reduce unsold inventory and eliminate obsolete inventory.
- Locally-sourced materials keep production times shorter and reduce lead times to customers.
- Low inventory levels require less working capital. They also cut storage costs.
Storing extra inventory and supplies gets expensive. Buying only what’s needed in a JIT system helps business owners control expenses. It also helps reduce waste by only making enough for forecasted orders. For example, a 1980s case study at Hewlett-Packard found an inventory reduction of 75% and up to 80% reduction in scrap.
This results in reduced unsold inventory. Allowing businesses to quickly pivot when manufacturing new products.
Adopting a JIT inventory management system proves to be helpful. But it needs a few components to be successful:
- An accurate demand forecasting system that updates frequently.
- Local, reliable suppliers who can provide small frequent orders.
- Efficient production and shipping schedules.
Without these things, a JIT system could easily become a logistical nightmare. Demand forecasting takes the guesswork out of what to order and produce.
Solid relationships with local suppliers shorten shipping times and make it easier to predict lead times. Everything needs to be on schedule. If a startup time delay hits part of the manufacturing process, the final product gets delayed too.
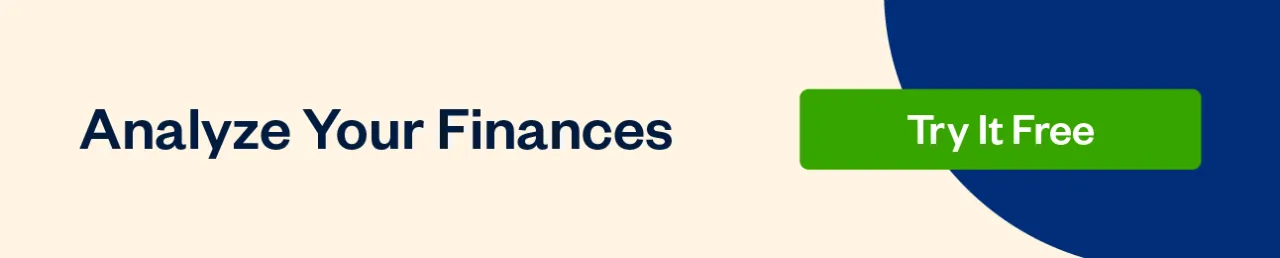
Advantages and Disadvantages of JIT
The advantages of JIT are that it reduces inventory and production costs. This allows companies to be lean and agile. Only making what’s needed eliminates huge back stocks of obsolete products. This allows the business to pivot quickly with industry or market changes.
JIT production also improves customer service by reducing lead times and cycle times. In turn, this increases customer satisfaction.
The process of implementing a JIT inventory system may initially create a decrease in quality control and an increase in defects. An important part of using this strategy is reworking the parts that are less efficient. Over a time period, reworking the process creates more efficiency in the production line and supply chain.
After working the snags out, you’re left with fewer product defects and improved quality control.
JIT also causes problems with production schedules. It’s difficult to predict when parts will arrive at their destinations in time. Getting materials from many suppliers within your timeframe is a logistical feat. It requires an accurate sales forecasting system to be effective. You may also need to invest in technology to link your system with your suppliers to coordinate deliveries.
Ordering supplies with the JIT method doesn’t leave room for supply chain disruptions. A heavy increase in demand causes trouble too. Without the materials on hand to meet demand, it can cost the business money in the long run.
Lastly, JIT can be very expensive if there is not enough capacity available or if a supplier cannot get the parts delivered on time.
What If Things Don’t Arrive in Time?
When the materials don’t arrive on time your production schedule gets delayed. Waiting for delayed materials impacts customer satisfaction and storage costs for other supplies.
This results in a loss of money for the business and being temporarily thrown off balance.
The most recent example of this was in 2020 when the production of hand sanitizer, masks, and antigen tests became scarce due to supply chain issues. The huge increase in demand drove instances of panic buying, price increases, and shipping delays.
Having a small insular stock of supplies can help businesses weather unexpected changes.
Summary
The JIT inventory method is a helpful way to manage production that reduces waste, increases productivity and saves money. While it offers several advantages it doesn’t insulate well against supply chain disruptions or large increases in demand.
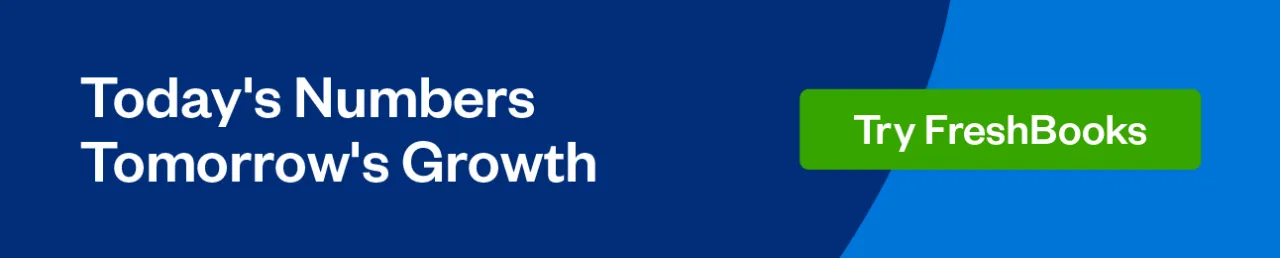
FAQs on Just-in-Time Inventory:
JIT inventory management is relatively simple. You don’t stockpile materials and products just in case. Instead, you order materials and create products as they’re needed.
A wide range of companies and businesses use JIT. Automobile manufacturers, book publishers, restaurants, and retailers have been known to use these strategies.
Just-in-time inventory has a big impact on the quality of goods. When appropriately done, it reduces defects in production. The focus is on producing goods to meet a need, rather than creating products just in case. So the production line catches more defects and reduces scrap.
Production employees are the most affected by the process of implementing JIT. They handle each of the supply orders, the increase in production, and the quality management.
JIT requires an existing order in place before producing goods. It might not work with businesses that see large fluctuations in demand or experience a lot of unpredictability.
Share: