How to Calculate Manufacturing Overhead Costs
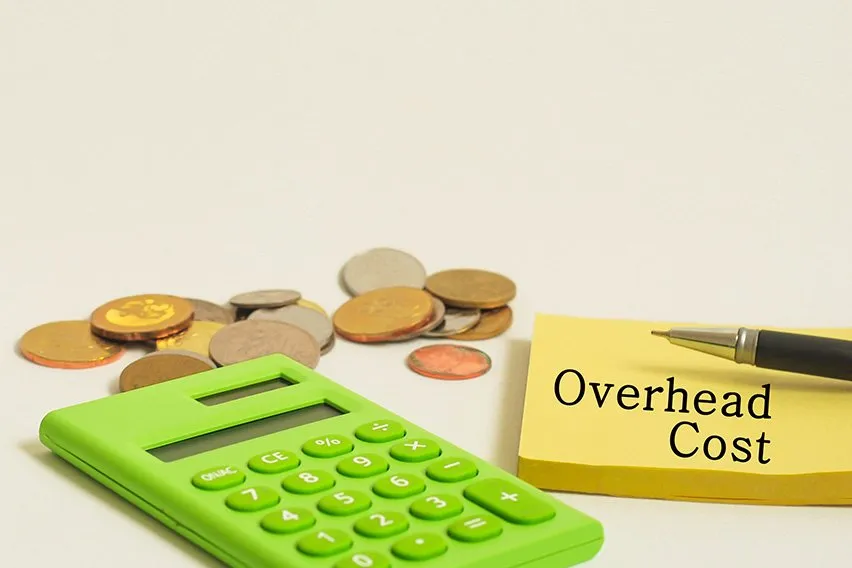
To calculate manufacturing overhead, you need to add all the indirect factory-related expenses incurred in manufacturing a product. This includes the costs of indirect materials, indirect labor, machine repairs, depreciation, factory supplies, insurance, electricity and more.
Manufacturing overhead is also known as factory overheads or manufacturing support costs. Overhead costs such as general administrative expenses and marketing costs are not included in manufacturing overhead costs.
What this article covers:
- What Is Included in Manufacturing Overhead?
- How to Calculate Manufacturing Overhead Rate?
- How to Account for Manufacturing Overhead?
- How Do You Calculate Allocated Manufacturing Overhead?
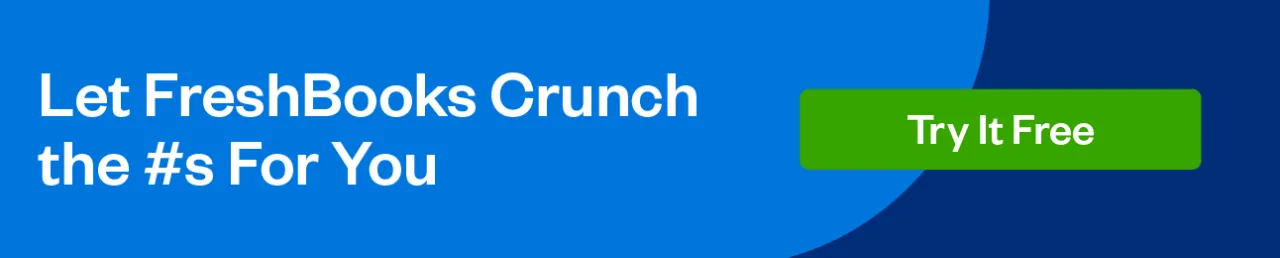
What Is Included in Manufacturing Overhead?
You need more than labor and raw materials to manufacture products. Manufacturing units need factory supplies, electricity and power to sustain their operations.
Examples of manufacturing overhead costs are:
- Rent of the production building
- Property taxes and insurance on manufacturing facilities and equipment
- Communication systems and computers for a manufacturing facility
- Depreciation on manufacturing equipment
- Salaries of maintenance personnel
- Salaries of factory management team
- Salaries of the material handlers
- Salaries of the quality control staff
- Factory supplies not directly associated with products
- Utilities for factory
- Janitorial staff wages
All the items in the list above are related to the manufacturing function of the business. These costs exclude variable costs required to manufacture products, such as direct materials and direct labor.
How to Calculate Manufacturing Overhead Rate?
Calculate the Total Manufacturing Overhead
To calculate the manufacturing overhead, identify the manufacturing overhead costs that help production run as smoothly as possible. Add all the indirect costs to calculate the manufacturing overhead.
Determine the Overhead Rate
Once youāve estimated the manufacturing overhead costs for a month, you need to determine the manufacturing overhead rate. This is the percentage that you must pay for overheads every month.
To compute the overhead rate, divide your monthly overhead costs by your total monthly sales and multiply it by 100.
For example, if your company has $80,000 in monthly manufacturing overhead and $500,000 in monthly sales, the overhead percentage would be about 16%.
Manufacturing Overhead Rate = Overhead Costs / Sales x 100
Manufacturing Overhead Rate = 80,000/500,000 x 100
This means 16% of your monthly revenue will go toward your companyās overhead costs.
If your manufacturing overhead rate is low, it means that the business is using its resources efficiently and effectively. On the other hand, a higher rate may indicate a lagging production process.
Determining the manufacturing overhead expenses can also help you create a budget for manufacturing overhead. You can set aside the amount of money needed to cover all overhead costs.
How to Account for Manufacturing Overhead?
According to the Generally Accepted Accounting Principles (GAAP) standards, the manufacturing overhead should be added to direct labor and direct materials costs to determine the cost of goods sold and the value of the inventory.
These costs must be included in the stock valuation of finished goods and work in progress. Both COGS and the inventory value must be reported on the income statement and the balance sheet.
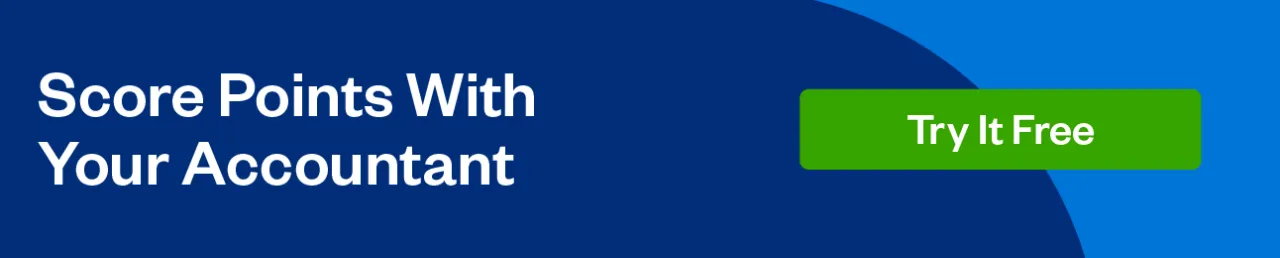
How Do You Calculate Allocated Manufacturing Overhead?
In order for a manufacturer’s financial statements to be in compliance with GAAP, a portion of the manufacturing overhead must be allocated to each item produced.
To allocate manufacturing overhead costs, an overhead rate is calculated and applied. When this is done in a precise and logical manner, it will give the manufacturer the true cost of manufacturing each item.
- Calculate the total manufacturing overhead costs. While some of these costs are fixed such as the rent of the factory, others may vary with an increase or decrease in production.
- Select an allocation base. The allocation base is the basis on which a business assigns overhead costs to products. The commonly used allocation bases in manufacturing are direct machine hours and direct labor hours.
- Divide the manufacturing overhead costs by the allocation base to calculate the amount of manufacturing overhead that should be assigned to each unit of production.
- Determine the total of the allocation base generated in the current period by reviewing the maintenance and payroll records of the factory. The payroll records, for example, will show 2,000 direct labor hours during the current period.
- Divide the allocation base value by the number of units produced. This provides the amount of manufacturing overhead attached to each unit of the allocation base.
For instance, if a factory has $2,000 in overhead costs and 500 direct labor hours, there is an overhead of $4 ($2,000 / 500) attached to each labor hour.
The allocation of costs is necessary to establish realistic figures for the cost of each unit manufactured.
Manufacturing overhead is an essential part of running a manufacturing unit. Tracking these costs and sticking to a proper budget can help you to determine just how efficiently your business is performing and help you reduce overhead costs in the future.
RELATED ARTICLES