Two-Bin Inventory Control: Definition & How it Works
Inventory control can be difficult.
But when the production process is simple and repetitive, manufacturers can take on what’s known as a two-bin inventory control system. But what exactly does the two-bin system do?
Read on as we take a closer look.
Table of Contents
KEY TAKEAWAYS
- Two-bin inventory control is a system that can be used to determine when current inventory levels need to be replenished.
- The first bin is the working stock, and the second bin is the reserve stock with excess inventory.
- Companies can figure out how much stock to keep based on historical data.
What Is Two-Bin Inventory Control?
Two-bin inventory control is a system that is used to figure out when the items or materials that are used in the production process should be replaced or replenished. It is an effective inventory management method for managing stock levels.
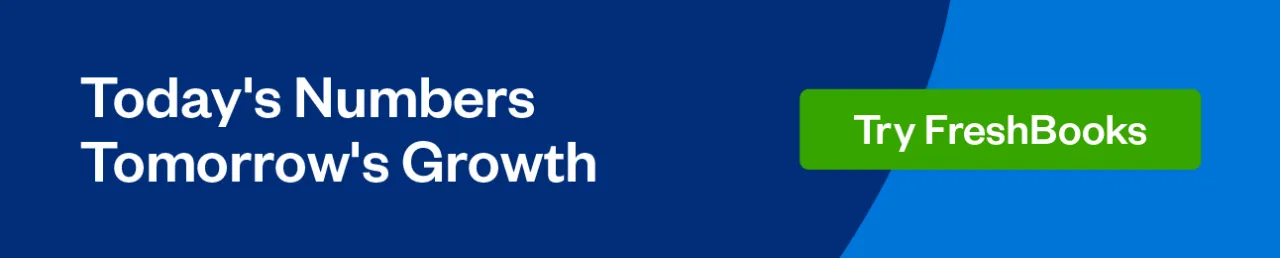
How Two-Bin Inventory Control Works
The two-bin system works so that when the items that are in the first bin have been used up, an order is placed to replace or refill them.
The second bin is then designed to have enough items or material to last until the order for the first bin is completed and delivered. So essentially, the first bin has a minimum of working stock, and the second bin has a working reserve safety stock.
How Is the Two-Bin Inventory Control Method Used?
Two-bin inventory control will almost always be used for low-value items or small items. These are items that can be stored in bulk and easily purchased. This is in contrast to the perpetual inventory system which deals with high-value, expensive inventory items.
The most typical way for it to work is based on the historical patterns of variance when it comes to the depletion rate of the stock from the first bin. Therefore, the amount that is ordered for the reserve stock in the second bin can be adjusted according to shifts in demand.
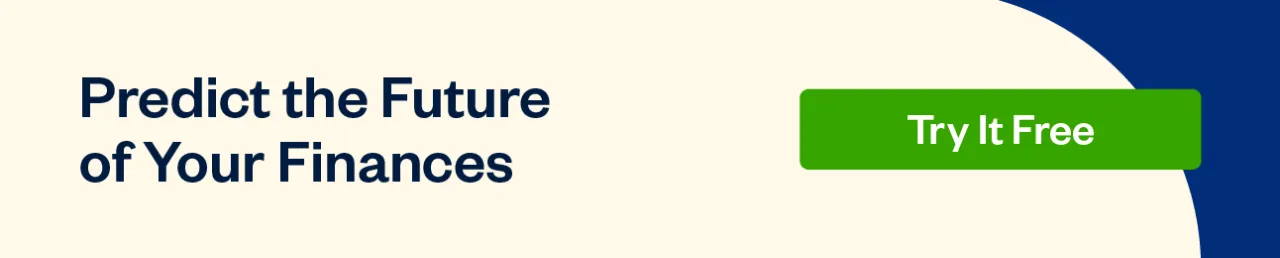
Two-Bin System Advantages and Disadvantages
Advantages
The two-bin inventory management system has a number of advantages, including:
- There is a faster, more reliable, and predictable ordering process.
- There is a reserve of products in case of a spike in demand.
- The simplicity of checking inventory and inventory tracking when levels are low.
- This system has less chance of overordering and loss.
Disadvantages
While there are some great advantages, there are also disadvantages. These include:
- Demand changes may cause issues as this method assumes a stable and repetitive production plan.
- This system does not suit a varied production line with extensive inventory. It is more suited to single product development.
- A lack of quality control.
Example of Two-Bin Inventory Control
Let’s say that Company X is a manufacturer that creates a product that has heavy usage of metal nails. It uses roughly 1,000 nails per week or roughly 200 per day. It also has a lead time of three days.
So Company X takes the daily usage and multiplies it by the lead time, meaning that the reserve bin should have a safety stock of at least 600 nails.
The company is aware that usage levels of the nails can fluctuate by as much as 20%. So as a precautionary measure, they choose to add 20% more nails to the reserve storage bin. This stock will then come in handy if there is a surge in demand and the production rate increases.
Summary
Two-bin inventory control is an effective inventory approach for single production lines. It benefits manufacturers that make singular products with a repetitive production schedule and production quantity.
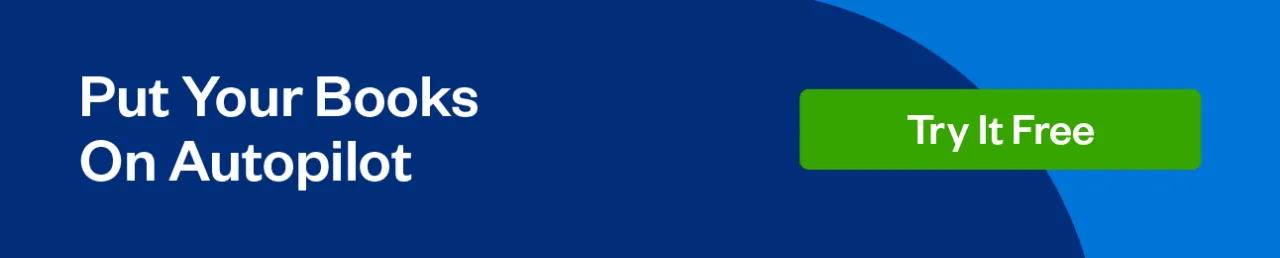
FAQs About Two-Bin Inventory Control
There are many benefits of a two-bin system. Such as quantity control, an easy ordering process, and the ability to have a reserve of products.
A single bin system is an inventory control system that depends on replenishing supply at a fixed time, rather than at a minimum stock level.
The term “Kanban” is another name for the two-bin system, so there is no difference.
Share: