Difference Between Activity Based Costing Vs Traditional Costing
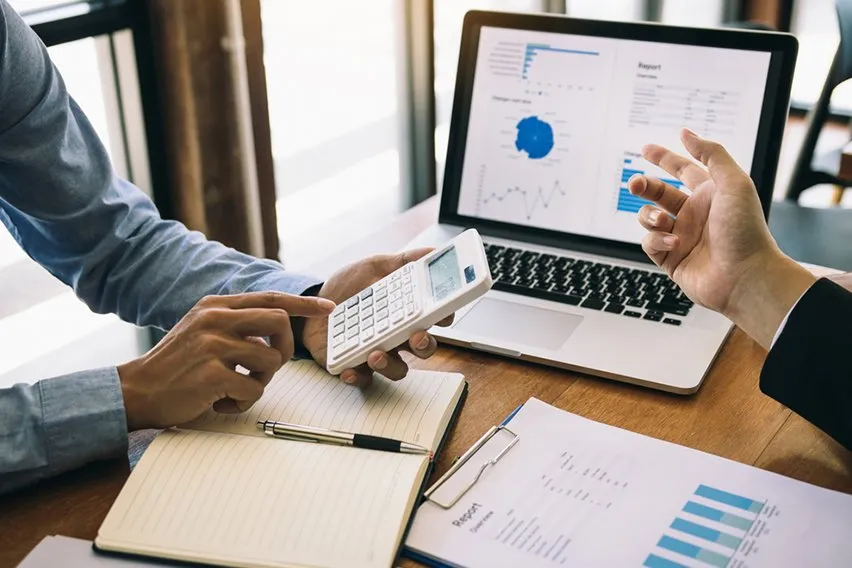
One of the most integral, and (for some) least fun, aspects of owning a business is accounting. For a business to be successful, you must be able to account for, or track, the cost of your operations. The most commonly used systems to do so are activity-based costing and traditional costing. To put in the plainest of terms, activity-based costing will set you back a few more dollars, but it is easier to understand than traditional costing. But, while traditional costing might be cheaper, it may be less accurate than traditional costing.
Trying to figure out which method is best for your business? You’ll need to determine the specific needs for your business and the uses for cost accounting. Then you can select the right costing method for you. It may come down to how many goods or services you offer, or if you’re aiming for accuracy or speed. We’ll break down all the pros and cons for you below.
Here’s What We’ll Cover:
What Is Activity-Based Costing?
How Activity-Based Costing Works
Pros And Cons Of Activity-Based Costing:
Pros And Cons Of Traditional Costing:
How Do I Know Which Works Best For Me?
What Is Activity-Based Costing?
Activity-based costing is also known as ABC costing. The ABC system works by identifying activities in an organization. Those activities are then assigned a cost to each product or service.
ABC costing is an approach to monitoring and costing business activities. This approach involves tracing the consumption of resources and costing final outputs. It is also defined as an accounting method that identifies a firm’s activities. Once identified, indirect costs are then assigned to objects.
ABC costing is based on George Staubus’ Activity Costing and Input-Output Accounting. This method was developed in the United States in the 1970s and 1980s, and it was a popular method from the uptake. That is until companies started using alternative methods like ‘Kaplan’s balanced scorecard’ in the 1990s.
At its core, ABC costing focuses on cost allocation and helps to separate fixed costs from variable costs and overhead costs. Splitting the costs helps identify cost drivers, which makes labour and materials easier to trace to products.
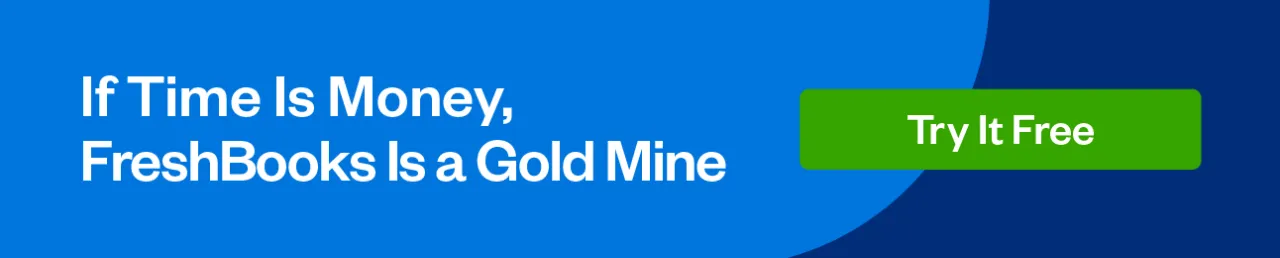
How Activity-Based Costing Works
STEP 1: Identify ABC costing needs and determine if the method is the right fit for an organization.
STEP 2: Set up basic training in ABC costing for employees and senior managers.
STEP 3: Define the project scope and identify objectives.
STEP 4: Pull out activities and drivers and determine what drives which activities.
STEP 5: Draw it out: create a cost and operational flow diagram that shows how resources connect to products and services offered.
STEP 6: Compile data showing operational relationships.
STEP 7: Build a software model off data.
STEP 8: Determine results, compile the report.
STEP 9: Combine reporting with data collection.
What Is Traditional Costing?
Traditional costing systems set itself apart by assigning expenses to an average overhead rate. Accountants then calculate this rate by combining all indirect costs and applying them in one common unit. Accountants then calculate the cost of each product or service by using the same rate. In simpler terms: traditional costing predicts profits by using cause-and-effect techniques.
Traditional costing is a method that relies on the addition of a proportion of overhead costs to direct costs to meet a total product cost.
This system relies on three basic steps:
- Accumulating costs
- Allocating non-production costs
- Allocating the resulting production department true costs to various products services or customers
This costing system is one that assigns the expected or standard costs. Other systems assign the actual costs of direct material, labour, and manufacturing overhead to a product, or a single cost driver.
Businesses have used the traditional costing method since the early 20th Century. Back then, direct labour and materials were the largest costs associated with running a business. There was little automation, and overhead costs were a much smaller percentage of total costs than they are now. It was an ideal method of costing for companies that offered only a few products or services.
Traditional costing stayed popular as automation picked up steam. Owners continued measuring their cost objects this way even as their overhead grew. This led accountants to find the glaring shortcomings of traditional costing. This was especially obvious with companies with larger overhead costs and more goods and services. Then, activity-based costing began to emerge as a way to more accurately divide a businesses’ costs.
At its core, traditional costing uses estimated overhead rates for a specific cost driver. These can include managerial expenses, packaging, machine hours, or maintenance.
How Traditional Costing Works
STEP 1: Identify overhead costs associated with production that don’t directly impact the product.
STEP 2: Estimate overhead costs for a specific time.
STEP 3: Select a single cost driver to use in calculations.
STEP 4: Estimate the time for the cost driver.
STEP 5: Calculate the predetermined overhead rate.
STEP 6: Multiply the predetermined overhead rate by your chosen metric for an estimated overhead cost.
Pros And Cons Of Activity-Based Costing:
Pros:
You’ll get a realistic picture of the costs of manufacturing specific products.
More accurately allocates manufacturing overhead.
Points out unnecessary costs.
Can spot a lagging production process and show specific targets for improvement.
Paints a clearer picture of costs in manufacturing overhead.
Gives more accurate profit margins.
Cons:
ABC costing is very time-consuming and expensive to maintain.
Heavier cost burden to compile and analyze data.
May be difficult to track down source data to run costs.
ABC reports can’t be used for external reporting because they often don’t follow accepted accounting principles.
Data may conflict with data compiled from traditional costing methods.
Pros And Cons Of Traditional Costing:
Pros:
Less complex than ABC costing.
More cost-effective than ABC costing.
More widely understood internally.
Easy to convey externally thanks to a more clear way to assess the value of products or services compared to ABC costing.
Cons:
A less precise method due to using less detailed information.
Not as helpful when it comes to identifying how to reduce waste.
Leaves no room for surprise costs.
Too simplified for many of today’s businesses with a myriad of products or services.
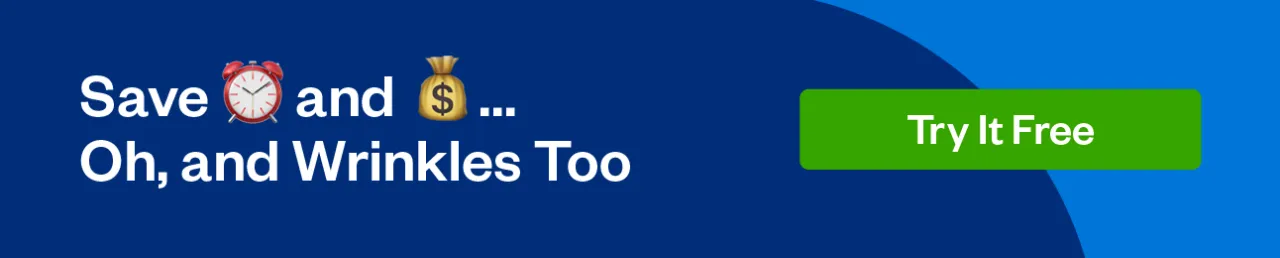
How Do I Know Which Works Best For Me?
When To Rely On Traditional Costing:
If you are tight on time, then traditional costing may be the right choice for you. This method is much less time-consuming than its counterpart, ABC costing.
If you want to make sure you know exactly what your costs are, then traditional costing will work well for you. You won’t need to worry about estimating any variables or calculating anything.
However, if you want to see where you could save money, then ABC costing might be the better option. You can easily identify areas where you could cut back on spending without sacrificing quality.
What If I Don’t Have The Time Or Money To Implement Both Methods?
Are your indirect costs lower than your direct costs? Sometimes this happens when production uses more hands-on labour than machine labour. Or it occurs when a company produces only one product, traditional costing may be a better solution for your company.
Many companies rely on traditional costing when it pertains to external reporting. Outside sources may not need such an accurate representation of costs, and estimates might be all you need to get the point across. If that’s the case, traditional costing may provide you with all you need. Leave the uber-detailed accounting that ABC costing provides for an internal report.
When To Rely On Activity-Based Costing:
ABC costing may not be the right fit for companies with smaller overheads in proportion to total operating costs. But the attention to detail will be exactly what you need when accuracy in a certain report is crucial. If you need a closer look at a myriad of costs, such as managerial and administrative, ABC should be your go-to.
If your indirect costs are higher than your direct costs. For some companies, relying on automated production rather than direct labour makes ABC a perfect fit for looking at a clear picture of costs.
Many companies turn to ABC costing when compiling internal reports. External reports often don’t need every detail broken down, while internal reports often do. ABC costing may be a good fit if you’re looking to identify any weak spots in your decision-making.
If your company only produces a few products or services then traditional costing maybe your best bet. But, if your company offers many different products or services, the more precise ABC costing method might be a better fit. If you’d like a detailed look at your finances, or to determine where to cut costs, ABC costing will help you understand the cost flow of your business.
Key Takeaways
Many businesses will use both methods of costing depending on the intended audience of the report. Put simply, ABC costing may be the right method for you if you’re looking for a detailed peek inside of the costs required in running your business. Traditional costing will give you the best bang for your buck if you don’t have as much time to dedicate to the report and you’re okay with less accuracy.
Enjoyed reading this article? Check out Resource Hub for more articles like this!
RELATED ARTICLES